What to Look for in a Flow Wrapper?
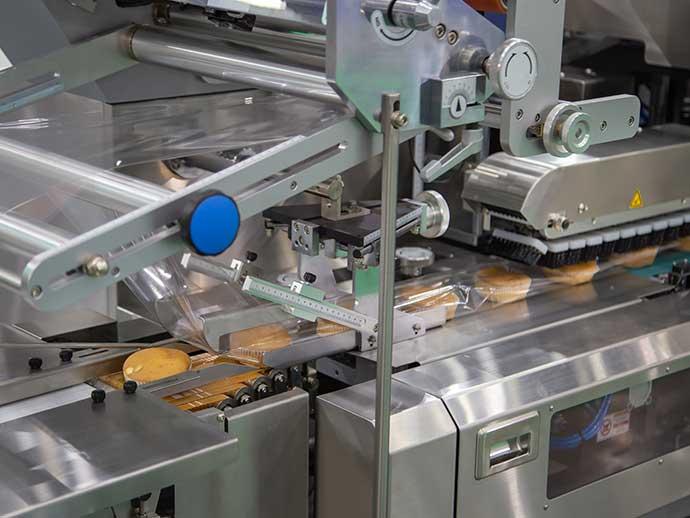
When choosing a flow wrapper for your packaging needs, there are several important factors to consider. Here’s a guide to help you make an informed decision.
The 3 things that you need to work together to make a successful packaging machine purchase.
1: Product that is being packaged. Make sure that the product is uniform in shape and size. The closer in size that the product is the better. Make sure the distance between pushers is sufficient. Remember the machine can run at a fast speed and consider that the worker can keep up for the length of their shift.
2: The Packaging Machine. Make sure that the machine your purchasing is designed for your product or products. Don't use a machine that is maxed out on the product size ether too small or too large. The machine will work better if the product is not too big or small.
3: The Packaging Film. Make sure that the film is compatible with your product and machine. the adjustments of the machine needs to be able to work with the film that your using. If the film is to thin or thick it could need different jaws or former to work efficiently. Not all film will work with all machines.
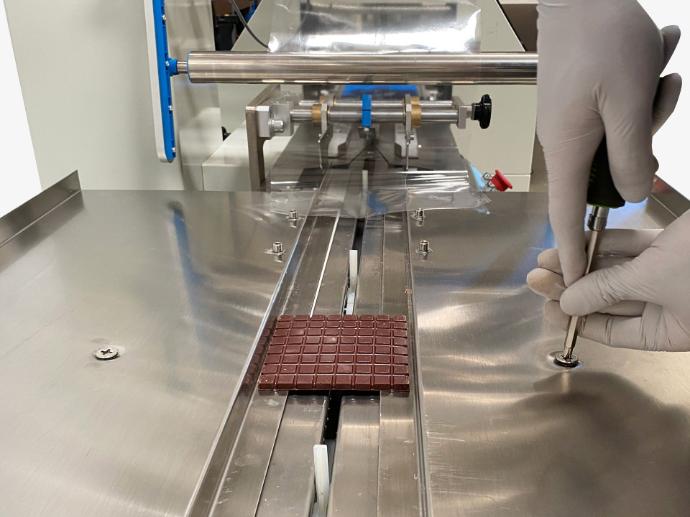
Product Compatibility
Size Shape: Ensure the flow wrapper can handle the dimensions of your products, whether they are irregularly shaped or standard.
Fragility: If your products are fragile or require gentle handling, make sure the machine offers appropriate adjustments and features to prevent damage.
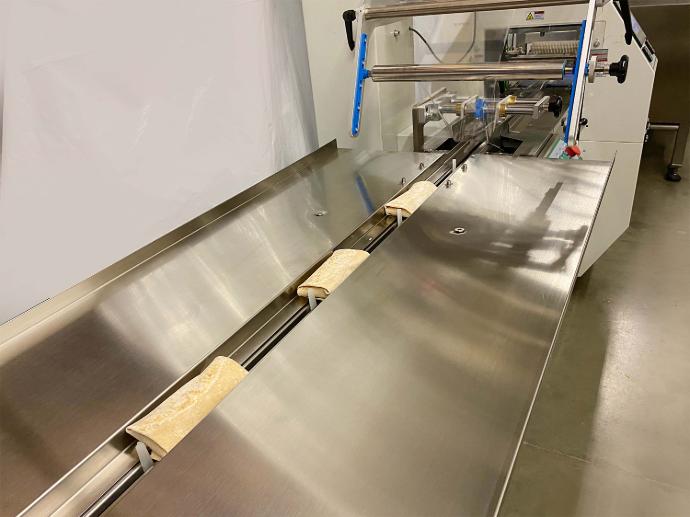
Speed Throughput
Packaging Speed: Consider the machine’s speed (measured in packages per minute). Ensure it matches your production requirements for volume and efficiency.
Adjustable Speeds: Look for machines with adjustable speed settings to accommodate different production needs or product types.
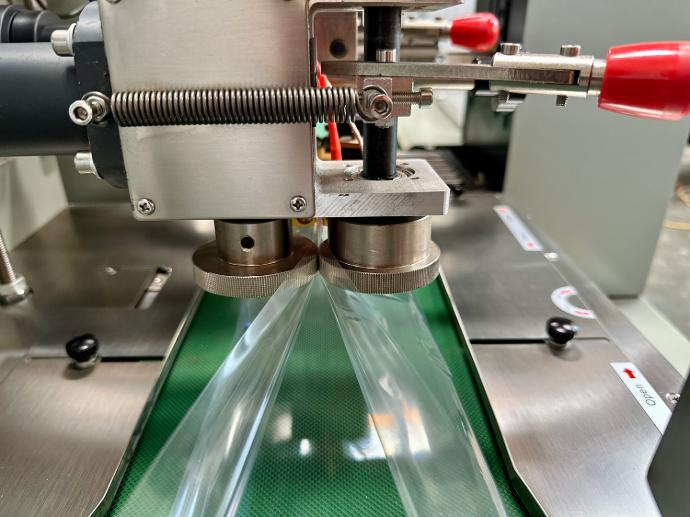
Sealing Technology
Seal Quality: The machine should provide consistent, airtight seals to ensure product freshness and protection. Check if it offers both fin seals and end seals.
Temperature Control: Ensure it has independent mid-sealing and end-sealing temperature controls to handle different film types accurately.
Sealing Precision: A photoelectric sensor for tracking color marks ensures precise cutting and sealing for consistent package quality.

Film Compatibility
Film Type: Make sure the flow wrapper is compatible with the type of film you use, such as polypropylene, polyethylene, or barrier films for specific applications (e.g., perishable foods).
Roll Stock Capacity: Verify that the machine can handle your roll stock's core diameter and width to ensure smooth operation.
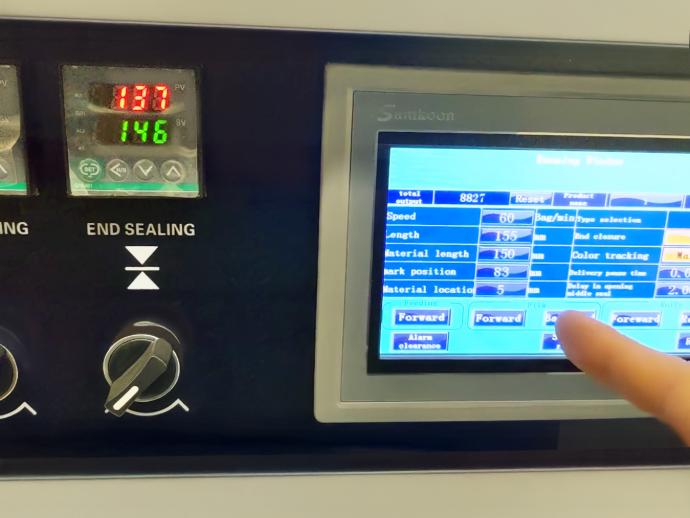
Ease of Operation
User-Friendly Interface: Look for a machine with an easy-to-use control panel and intuitive settings for package length, speed, and sealing adjustments.
Quick Changeover: Ensure the machine allows for fast and simple changeovers between different product sizes or types to minimize downtime.
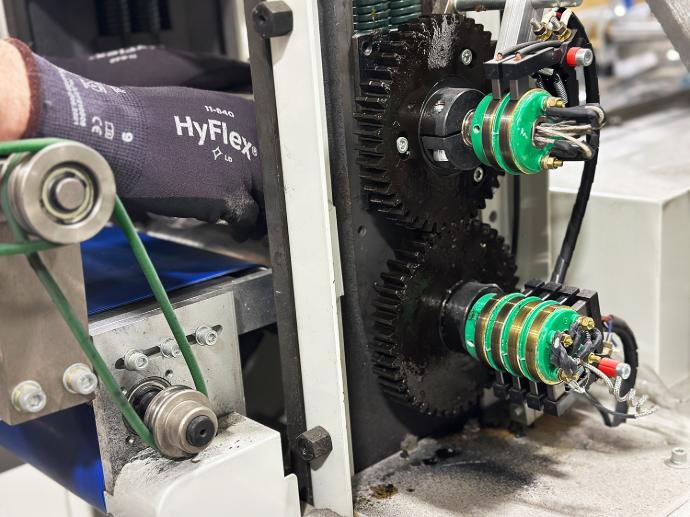
Machine Reliability
Durability: Opt for a machine with a robust build and high-quality components to ensure longevity and minimal maintenance issues.
Ease of Maintenance: Choose a flow wrapper that provides easy access to key parts for cleaning, lubrication, and repairs. Machines with self-diagnostic features can alert operators to potential issues before they cause downtime.
Spare Parts Availability: Check that replacement parts are readily available to minimize downtime if something needs repair or replacement.
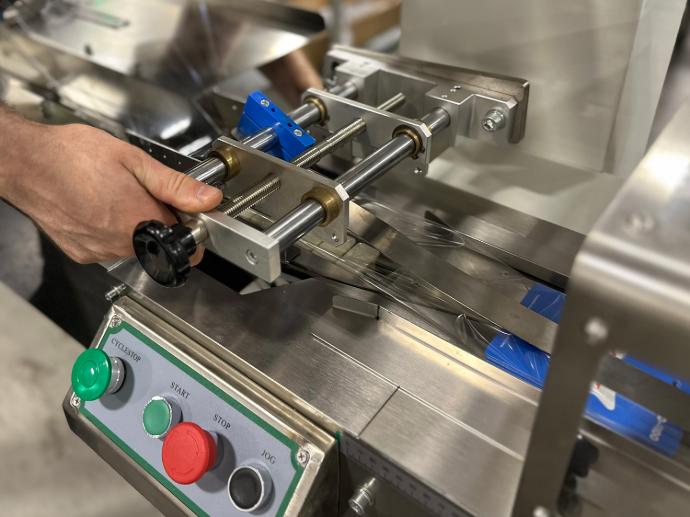
Flexibility
Adjustable Settings: Machines with customizable settings for bag length, film tension, and sealing parameters allow you to adapt the wrapper to various product lines.
Optional Features: Consider additional features like gas flushing (for modified atmosphere packaging), date or code printing, or product collating systems if needed for your production.
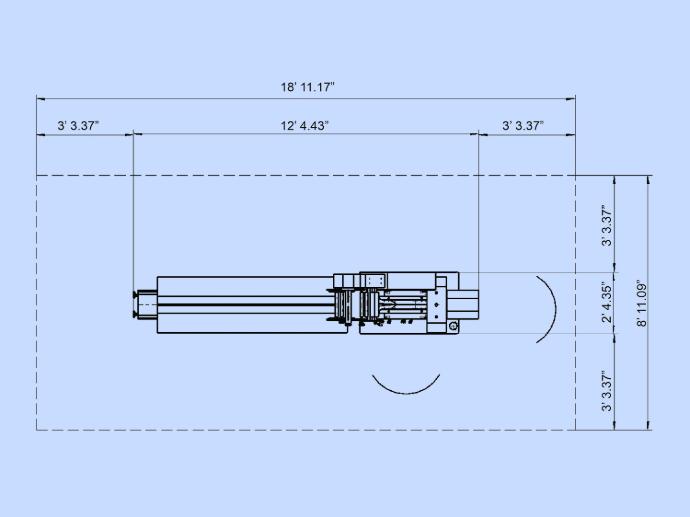
Size Footprint
Space Requirements: Make sure the flow wrapper fits within the available space on your production floor, and consider the layout of surrounding equipment.
Portability: If you need flexibility in your workspace, check if the machine can be moved or reconfigured easily.
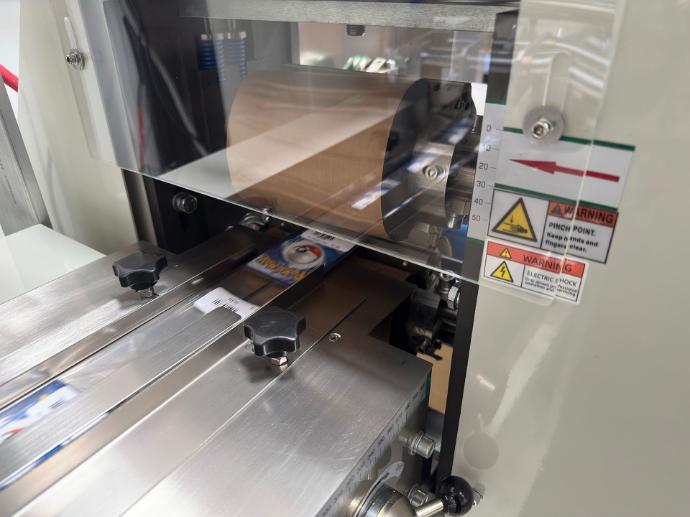
Safety Features
Emergency Stop: Ensure the machine has a clearly accessible emergency stop button.
Guards and Shields: Check for protective guards around moving parts to prevent operator injury.
Automatic Diagnostics: Machines equipped with intelligent diagnostics can detect and alert operators to potential faults, improving safety and reducing downtime.