Check Product Alignment
Ensure your products are correctly aligned on the infeed conveyor. Misaligned products can lead to jams or improper sealing.
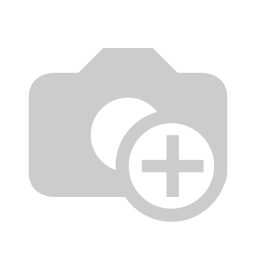
Adjust Infeed Timing
Verify that the timing between the infeed conveyor and the film feed is synchronized. Incorrect timing can cause wrapping errors.
Inspect Conveyor Belts
Check for worn or misaligned conveyor belts, which may cause inconsistent feeding. Adjust or replace the belts as necessary.
Clean Sensors
Dust or debris on sensors can cause faulty product detection. Use a soft cloth to clean sensors and ensure they are operating correctly.
Check Product Size and Shape
Ensure that the product dimensions match the machine's specifications. Irregular or oversized products can interfere with feeding.
Examine Film Tension
Incorrect film tension can misalign the film and affect product wrapping. Adjust the tension for smooth and even feeding.
Need Help?
Still having trouble? Contact our technical support team for expert assistance.
Contact Us